Basic Stance
Advantest effectively combines three different production methods: all-in-house production, EMS production by a company that handles the entire supply chain, and outsourcing to partners that handle only the manufacturing of products. With the slogan Design for Supply Chain (DfSC) in mind, we aim to build a manufacturing system that is resilient to supply-demand fluctuations and BCP, while exploring ways to maximize the benefits of each method.
The Gunma Factory, our in-house production facility, is evolving into a “mother factory” that operates the entire manufacturing process in collaboration with our outsourcing partners. Now, we have expanded the ratio of outsourced production to more than 80%.
A cooperative relationship with our business partners is essential for developing the best supply system based on three different production methods. Advantest upholds fair business relations in accordance with relevant laws and regulations while maintaining close communication with our business partners.
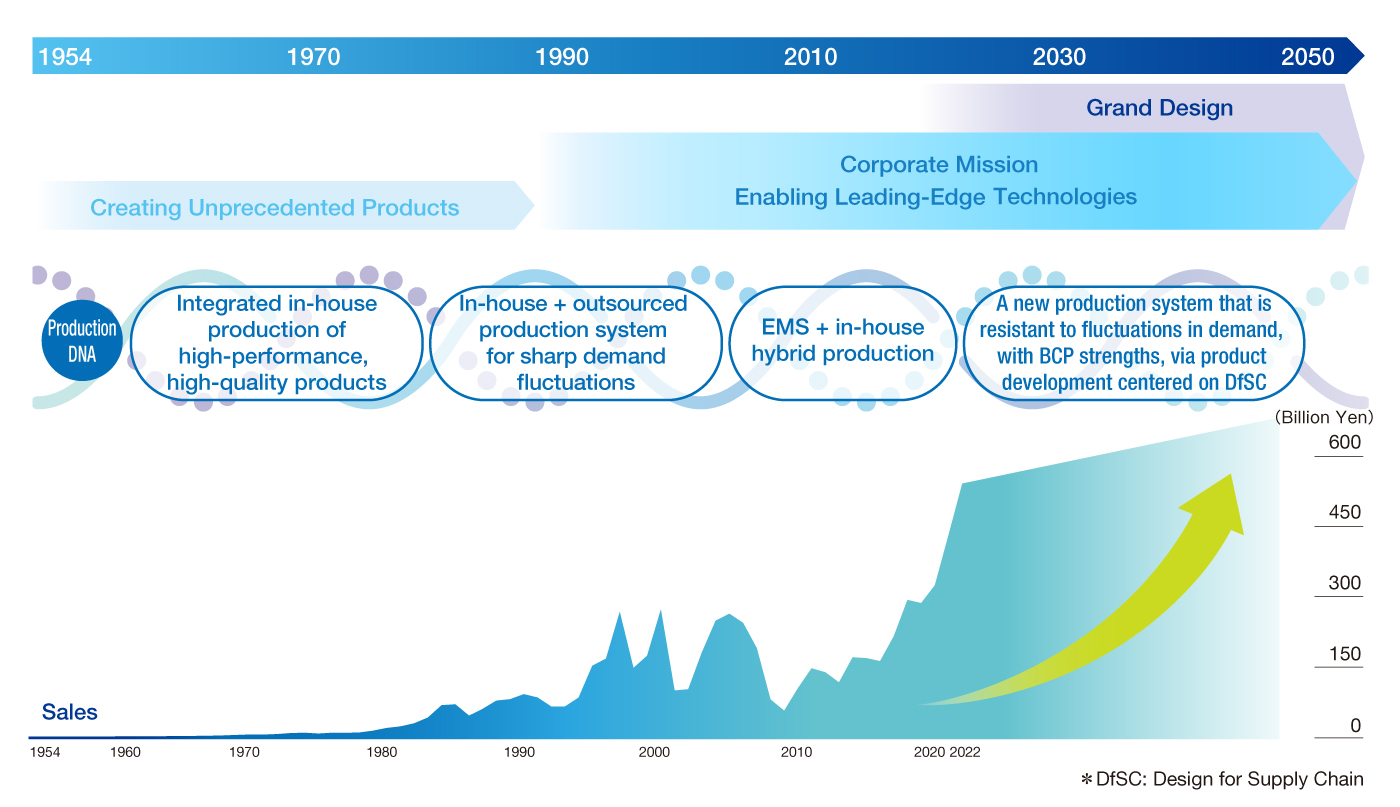
Procurement Policy
Advantest upholds collaboration and cooperation with our suppliers, who are our important stakeholders, to build a sustainable supply chain that considers environmental, social and ethical considerations through comprehensive engagement activities, as stated in its Sustainability Policy. We place value on open communication with our business partners, which will ultimately lead to building trusting relationships and mutual development.
In order to maintain fair business relationships in accordance with relevant laws and regulations, we have established a Procurement Policy, to which we have shared and sought cooperation from our suppliers. We have also prescribed the Supply Chain CSR Promotion Guidebook and Green Procurement Guidelines, and endeavor to build a supply chain with the need to respect human rights, occupational safety, and environmental considerations.
Supply Chain Management System
Advantest's Supply Chain Division and Global SCM Center of the Production Group, headed by the Chief Production Officer (CPO), are responsible for formulating and implementing procurement, outsourcing, logistics strategies, and other additional services. Moreover, we procure parts, which have been certified by each global base, in a timely and appropriate manner based on globally standardized evaluation criteria for parts selection.
In addition, the Supply Chain Division regularly reports key procurement strategies and activity results to the Executive Committee. The Board of Directors and the Audit and Supervisory Committee are also informed annually of key procurement strategies, as well as items identified in the previous year and the status of responses to them. Feedback from the Audit and Supervisory Committee is reflected in the following fiscal year's activities.
Policies are deliberated and decided by the Unit ESG leaders of the Sustainable Management Promotion Working Group in the Supply Chain Division under the direction of the CPO. Policies and guidelines are reviewed once a year, as they need to be revised depending on global trends. Any changes to policies and guidelines are reported to the Board of Directors by the CPO after approval by the Executive Committee.
Updated policies are published on our website and notified to suppliers via a dedicated tool.
In July 2024, the head of the organizational structure was replaced from CPO to Chief Supply Chain Officer (CSCO). As the next step in strengthening supply chain operations, we will aim to achieve the Grand Design by transforming supply chain operations from an internal process-driven to a market and customer-driven approach.
Measures against procurement risks
Procurement risks due to supply chain uncertainties such as climate change, natural disasters, and geopolitical risks persist. On top of the ongoing visualization of the factory (visualization of processes and information from parts procurement to production and shipping), we have established a system to predict supply-demand balance in real time to enable prompt and appropriate response. Furthermore, at our global bases, the CPO is spearheading partnership agreements with our suppliers, exchanging information at the top level, and boosting cooperation with EMS.
Advantest promotes procurement from multiple companies in principle as a contingency for the procurement of components from the perspective of BCP. In FY2022, we created a BCP map of our suppliers and manufacturing bases to speed up information collection and countermeasure examination in case of a disaster.
Education for Implementing Fair Trade
Advantest offered education on the Act against Delay in Payment of
Subcontract Proceeds, etc. to Subcontractors for all employees of
group companies in Japan, along with company-wide compliance
education. As a result, we saw an upliftment of the levels of
consciousness among all employees in Japan, irrespective of the
department they belong to.
Going forward, we will continue to
maintain fair trade through ongoing employee education and individual
support.